FAQ
Mold failure of the basic reasons and preventive measures!
1 die failure
Hot and cold mold in service in the basic form of failure can be divided into: plastic deformation; wear; fatigue;
(1) plastic deformation.
Plastic deformation that bear the load is greater than the yield strength of the deformation. Such as die cavity collapse, hole expansion, angular collapse and punching upsetting, longitudinal bending and so on. In particular, hot work die, the working surface and high temperature material contact, so that the cavity surface temperature is often more than hot work die steel tempering temperature, groove wall due to softening was crushed or pressure heap. Low hardenability of steel for cold heading die, the mold in the quenching and heating, the inner hole of the water cooling to produce a hardened layer. Mold in use, such as cold heading force is too large, hardened layer below the base compression yield strength is not high, the mold cavity will be crushed. The yield strength of the mold steel is generally increased with the increase of the content of carbon (c) from the increase of some alloying elements. When the hardness is the same, the compressive strength of the steel with different chemical composition is different. When the steel hardness is 63HRC, The following four kinds of steel yield resistance from high to low order: W18Cr4V> Cr12> Cr6WV> 5CrNiW.
(2) wear failure.
Wear failure refers to the edge of the door passivation, angular round, plane subsidence, surface groove marks, peel off the mucous membrane (in the friction mold table and stick some blank metal). In addition, the punch in the work, due to the combustion of lubricants into high-pressure gas, the punch surface of the scouring, the formation of cavitation.
If the load is not large, the type of wear is mainly oxidation, wear can also be a certain degree of bite wear, when the blade part of the blunt or stamping load is large, the situation of bite wear will become serious, and make Wear wear, mold steel wear resistance depends not only on its hardness, but also depends on the nature of the carbide, size, distribution and quantity, in the mold steel, the current high-speed steel and high chrome steel wear resistance is higher. However, in the presence of severe carbide segregation or large particles of carbides in the steel case, these carbides are easily peeled off, causing abrasive wear to accelerate wear. The impact of relatively light cold die steel (sheet blanking, stretching, bending, etc.), the load is not large, mainly static wear. In the static wear conditions, the mold steel carbon content, wear resistance is large. In the impact of wear conditions (such as cold heading, cold extrusion, hot forging, etc.), die steel too much carbide does not help improve wear resistance, but because of the impact of abrasive wear, and reduce wear resistance.
The results show that under the condition of impact abrasive wear, the carbon content of die steel is above the upper limit of O.6%. The cold heading die works under the impact load condition, such as too much carbide in the mold steel, Surface flaking. These exfoliated hard particles will become abrasive and speed up the wear. Hot mold cavity surface, due to high temperature softening and wear resistance to reduce, in addition, iron oxide also play the role of abrasive, as well as high temperature oxidation corrosion.
(3) fatigue failure.
Fatigue failure characteristics: some parts of Dongguan precision molds after a certain period of service, initiation of small cracks, and gradually extended to the depth, extended to a certain size, a serious weakening of the mold carrying capacity caused by fracture. Fatigue crack initiation in the stress of the larger parts, especially the stress concentration (size transition, notch, knife marks, wear cracks, etc.), fatigue fracture broken door in two parts, part of the fatigue crack development fatigue fracture section, Showing shell-like, fatigue source located at the top of the shell. The other part of the sudden fracture, showing uneven rough section.
So that the root cause of fatigue damage die for the special ring load, where the surface can increase the tensile stress factors can accelerate the initiation of fatigue cracks.
Cold work die in high hard state work, the mold steel has a high yield strength and very low fracture toughness. The high yield strength is beneficial to delay the generation of fatigue crack, but the low fracture toughness increases the fatigue crack growth rate and the critical length decreases, so that the fatigue crack propagation cycle is greatly shortened. Therefore, the fatigue life of the cold mold depends mainly on fatigue Crack initiation time.
Hot die is generally in the middle or lower hardness of the service, mold fracture toughness is much higher than the cold mold, therefore, in the hot die, the fatigue crack growth rate is lower than the cold mold, the critical length is greater than the cold The subcritical expansion period of the fatigue die is much longer than that of the cold mold, but the surface of the hot die is quenched and the hot and hot is easy to sprout hot and cold fatigue crack. The fatigue crack initiation time of the hot die is higher than that of the cold mold Which is much shorter, and therefore, the fatigue life of many thermal models depends mainly on the time of fatigue crack propagation.
(4) Fracture failure.
Fracture failure common forms are: chipping, teeth, splitting, breaking, cracking, etc., different mold fracture driving force is different. Cold work die, suffered mainly by the mechanical force (punching force). In addition to the mechanical force, there are thermal stress and tissue stress, there are many hot work die high temperature, and the use of forced cooling, the internal stress can be far more than the mechanical stress, so many thermal model The fracture is mainly related to the internal stress is too large. <
Mold fracture process there are two: one-time fracture and fatigue fracture. One-time fracture for the mold sometimes in the stamping suddenly broken, the crack once the initiation, after the instability, expansion. Its main reason is severe overload or mold material serious embrittlement (such as overheating, tempering, severe stress set and serious metallurgical defects, etc.).
2 mold failure reasons and preventive measures
(1) unreasonable structural design caused failure.
Sharp corners (stress concentration above the average stress more than ten times) and excessive cross-section changes caused by stress concentration, often become the source of many early failure of the mold. And in the heat treatment quenching process, the sharp angle caused by residual tensile stress, shorten the die life.
Precautions: The transition of the punch parts should be smooth and smooth, any small knife marks will cause a strong stress concentration, its diameter and length should meet certain requirements.
(2) mold material caused by poor quality failure.
(Such as oxidation, decarbonization, folding, scars, etc.) affect the performance of the steel, such as oxidation, shrinkage, shrinkage, inclusions, segregation,
A. Excessive inclusions cause failure.
In the presence of inclusions in steel, there are cracks in the mold, especially brittle oxides and silicates, which do not undergo plastic deformation during hot press processing and cause only brittle fracture to form microcracks. In the subsequent heat treatment and the use of secondary cracks in the further expansion, and cause the mold cracking. In addition, in the grinding, due to large particles inclusions off the surface hole caused.
B. Surface decarburization causes failure.
Die steel in the hot press processing and annealing, often due to the heating temperature is too high, holding time is too long, resulting in steel surface decarburization, severe decarburization of steel in the mechanical processing, and sometimes still remain decarburization layer, , Due to the different internal and external organizations (surface decarburization layer for the iron body, the internal pearlite) caused by organizational transformation is inconsistent, and cracks.
C. Carbide distribution is uneven, causing failure.
Crl2, Cr112MoV and other mold steel carbon content and alloying elements are high, forming a number of eutectic carbides, these carbides in the relatively small forging, easy to show band and network segregation, resulting in quenching often appear along the ribbon carbide distribution Of the crack, the mold in the use of cracks to further expand, resulting in mold cracking failure.
Precautionary measures: steel in the satin rolling, Dongguan mold design should be repeated multi-directional forging, so the eutectic carbide in the steel crushed more evenly, to ensure that the steel carbide unevenness level requirements.
(3) mold machine with improper.
A cutting of the knife marks: mold cavity parts or punch the fillet parts in the machining, often due to the ingestion of the knife leaving the local leaving the knife marks, resulting in serious stress concentration, when the quenching process should be Mountain concentrated parts are prone to microcracks.
Precautions: In the final cutting of parts roughing, should try to reduce the amount of feed, improve the mold surface finish.
B Electrochemical processing caused failure. Mold in the electrical processing, due to discharge produce a lot of heat, the mold will be processed parts of the heating to a very high temperature, the organization changes, the formation of the so-called electrical processing abnormal layer, in the abnormal layer surface due to high temperature melting, Fast solidification, the layer was white under the microscope, there are many micro-cracks inside the white layer under the area of quenching, called quenching layer, and then into the heat due to weakened, the temperature is not high, only tempering, called back Fire layer. Determination of cross-section hardness distribution: melting and then solidification layer, the hardness is high, up to 610 ~ 740HRC, the thickness of 30pu, quenching layer hardness of 400 ~ 500HRC, thick 20pu. Tempering is a high temperature tempering, the organization is soft, the hardness of 380 ~ 400HRC, thick 10pu.
Preventive measures: ① mechanical method to remove the open layer of re-solidification layer, especially micro-cracks; ② in the electrical processing after a low-temperature tempering, so that the abnormal layer stabilization, to prevent micro-crack expansion.
C grinding caused failure. Mold cavity surface grinding, due to grinding speed is too large, too fine grinding wheel or poor cooling conditions such as poor factors, will lead to grinding table overheating or cause surface softening, hardness reduction, so that the mold in use Wear serious, or thermal stress and produce grinding cracks, leading to early failure.
Preventive measures: ① the use of strong cutting force of the coarse grinding wheel or poor adhesion of the wheel; ② reduce the workpiece feed; ③ use the appropriate coolant; ④ grinding after 250 ~ 350 ℃ tempering, in addition to grinding stress The
(4) mold heat treatment process is not appropriate.
Heating temperature, the length of holding time, cooling speed and other heat treatment process parameters are not properly selected, will become a mold failure factor.
A. Heating speed: mold steel contains more carbon and cohesive elements, thermal conductivity is poor, therefore, the heating rate can not be too fast, should be slow to prevent Dongguan mold processing deformation and cracking. In the air furnace heating quenching, in order to prevent oxidation and decarbonization, the use of box protection heating, this time heating rate should not be too fast, and the heat should be slower. This will not produce a large thermal stress, relatively safe. If the mold heating speed, fast heat, mold inside and outside have a lot of thermal stress. If the control is improper, it is easy to produce deformation or cracks, must be used to warm up or slow down the temperature to prevent.
B. Oxidation and decarburization. Mold quenching is carried out at high temperatures, if not strictly controlled, the table is easy to oxidize and decarburize. In addition, the mold surface decarburization, due to differences in the inner and outer layers, the cooling occurs in the larger tissue stress, resulting in quenching cracks.
Preventive measures: can be used to protect the box, the box filled with anti-oxidation and decarburization of the filler material.
Cooling conditions
Different mold materials, according to the required state of the organization, the cooling rate is different. For high alloy steel, due to contain more alloying elements, high hardenability, you can use oil cooling, air cooling and even isothermal quenching and grade quenching and other heat treatment process.
Next:How to improve the life of the mold?
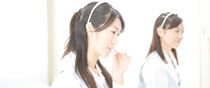
Hong'an Plastic
Mobile:18926888318
Phone: +86-0769-81186880
Fax:+86-0769-81186655
E-mail:[email protected]
Address:No.28 three road along Hexi Dongkeng Town, Dongguan City