Company News
Plastic mold injection principle
Plastic mold mainly by the casting system, forming parts and structural parts of three parts. Which is pouring system and forming parts are in direct contact with the plastic parts, and with the plastic and products and changes, is the most complex plastic mold, the largest change, requiring processing of the highest degree of finish and precision.
Plastic mold pouring system refers to the plastic from the nozzle into the cavity before the flow part, including the main channel, cold material, shunt and gate and so on. Molding parts are the various parts that make up the shape of the product, including dynamic mold, mold and cavity, core, forming rod and exhaust port.
First, the main channel
It is a mold in the injection nozzle to the nozzle or cavity of a channel. The top of the main flow path is concave to interface with the nozzle.
The main channel inlet diameter should be slightly larger than the nozzle diameter (0.8mm) to avoid the flash, and to prevent the two are due to convergence is not allowed to intercept.
Import diameter according to the size of the product, generally 4-8mm. The main channel diameter should be expanded inward at 3 ° to 5 ° angle, so that the flow of hair removal.
Second, the cold material points
It is a hole at the end of the main runway to catch the cold material produced between the two injections at the end of the nozzle, thereby preventing clogging of the manifold or gate. If the cold material is mixed into the cavity, the internal stress is liable to be produced in the article.
The diameter of the cold material is about 8 to 10 mm and the depth is 6 mm. In order to facilitate stripping, the bottom of the demolition of the pole is often born. The top of the demolding bar should be designed to be tortuous hook or set down trough, so that when the mold can be successfully pulled out of the main road.
Third, the diversion channel
It is a multi-slot mode to connect the main channel and the various cavity of the channel. In order for the melt to fill the cavities at equal velocity, the arrangement of the shunts on the mold should be symmetrical and equidistantly distributed. The shape and size of the cross-section of the shunt are affected by the flow of the plastic melt, the release of the product and the ease of mold making.
If the flow is equal, the flow resistance of the circular section is the smallest. But the cylindrical surface of the smaller than the surface of the bypass flow of the cooling of the negative, and this shunt must be set up in the two molds, both laborious and easy to align.
Therefore, it is often used in the trapezoidal or semicircular cross-section of the diversion channel, and opened with a mold on the mold half. The flow path surface must be polished to reduce flow resistance to provide faster filling speed. The size of the flow channel is determined by the size and thickness of the plastic variety, product.
For most thermoplastics, the cross-section width of the diversion channel is no more than 8m, large up to 10-12m, small 2-3m. To meet the needs of the premise should be to minimize the cross-sectional area, so as not to increase the diversion of hair and extended cooling time.
Four, gate
It is connected to the main channel (or shunt) and the cavity of the channel. The cross-sectional area of the channel can be equal to the main channel (or shunt), but is usually reduced. So it is the entire flow channel system in the smallest part of the cross-sectional area. The shape and size of the gate have a great influence on the quality of the product.
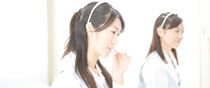
Hong'an Plastic
Mobile:18926888318
Phone: +86-0769-81186880
Fax:+86-0769-81186655
E-mail:[email protected]
Address:No.28 three road along Hexi Dongkeng Town, Dongguan City